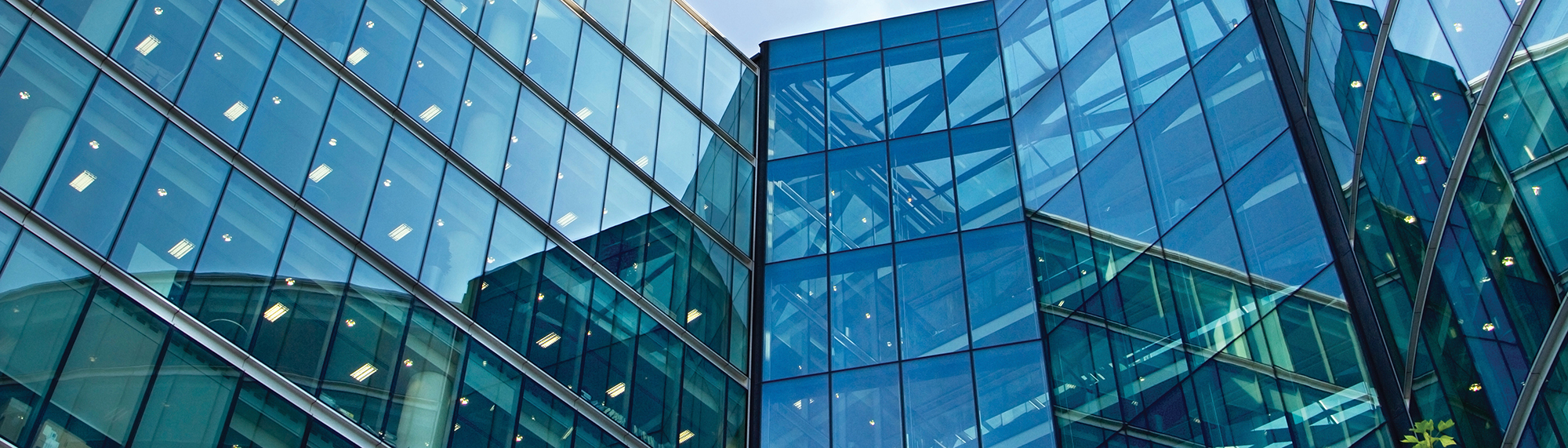
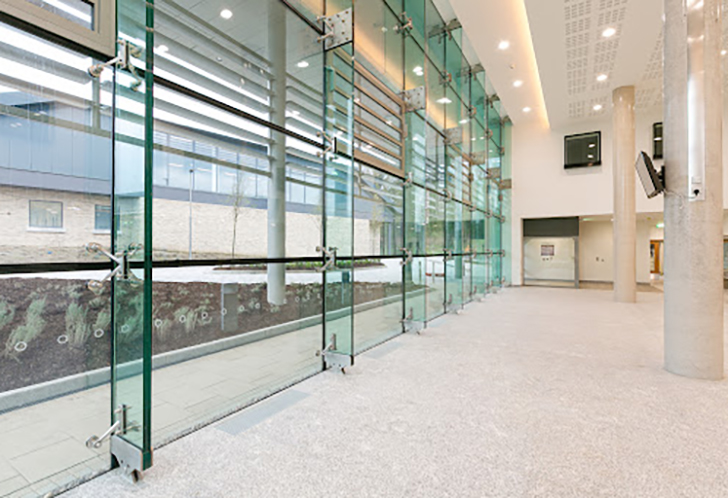
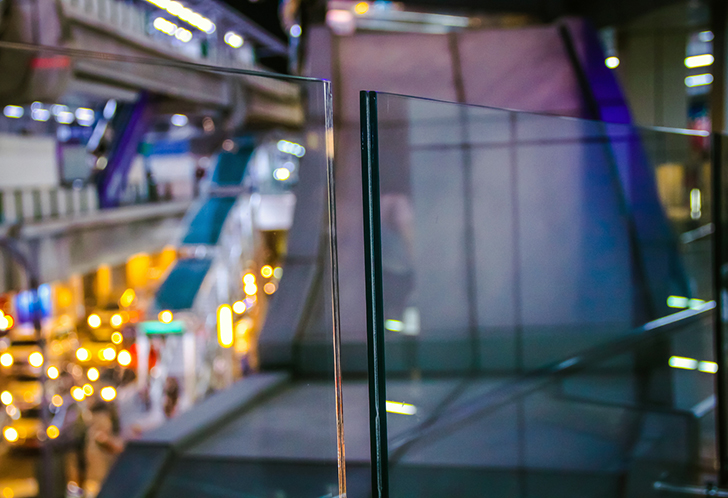
Laminated Glass
Laminated glass, sometimes called “lami,” is made by placing a layer of polyvinyl butyral (PVB) between two or more glass lites. The PVB can be clear or tinted, The entire unit is then fused under heat and pressure in a special oven called an autoclave. The laminating process can be performed on clear, tinted, reflective, heat-strengthened or tempered glass.
Laminated glass features:
-The plastic portion of laminated glass may be clear or tinted.
-Laminated glass aids in the screening of UV radiation.
-Laminated glass is beneficial for soundproofing.
-One of the biggest benefits of laminated glass is that if it does break, the broken glass will stick to the plastic rather than falling to the floor.
Laminated glass is used in safety glazing applications. However, it has many other applications, such as burglar resistance, sound reduction, sloped glazing and space enclosures. Laminated glass is used as the inboard lite in skylights. By varying the thickness and color of the PVB, laminated glass can be used to reduce the transmission of solar energy, control glare, and screen out ultraviolet radiation, similar to reflective glass.
Benefits of Laminated Glass
When laminated glass breaks, the glass particles adhere to the PVB and do not fly or fall. Certain combinations of glass and PVB thicknesses qualify as safety glazing materials under the health and safety standards set by the Australian Standard AS1288-2006.